Introduction
“Optimizing Reliability While Controlling Costs With Smart Predictive Maintenance”
Smart Predictive Maintenance is a strategic method to revolutionize operational reliability and cost efficiency in running power plants. With the power of data analytics as an approach to predict equipment failures before they occur, optimize maintenance schedules and minimize downtime.
This proactive strategy not only extends asset life but also ensures continued productivity, placing the business at the forefront of innovation and sustainability.
Proven Use Cases
Real case application of services
Predictive Maintenance
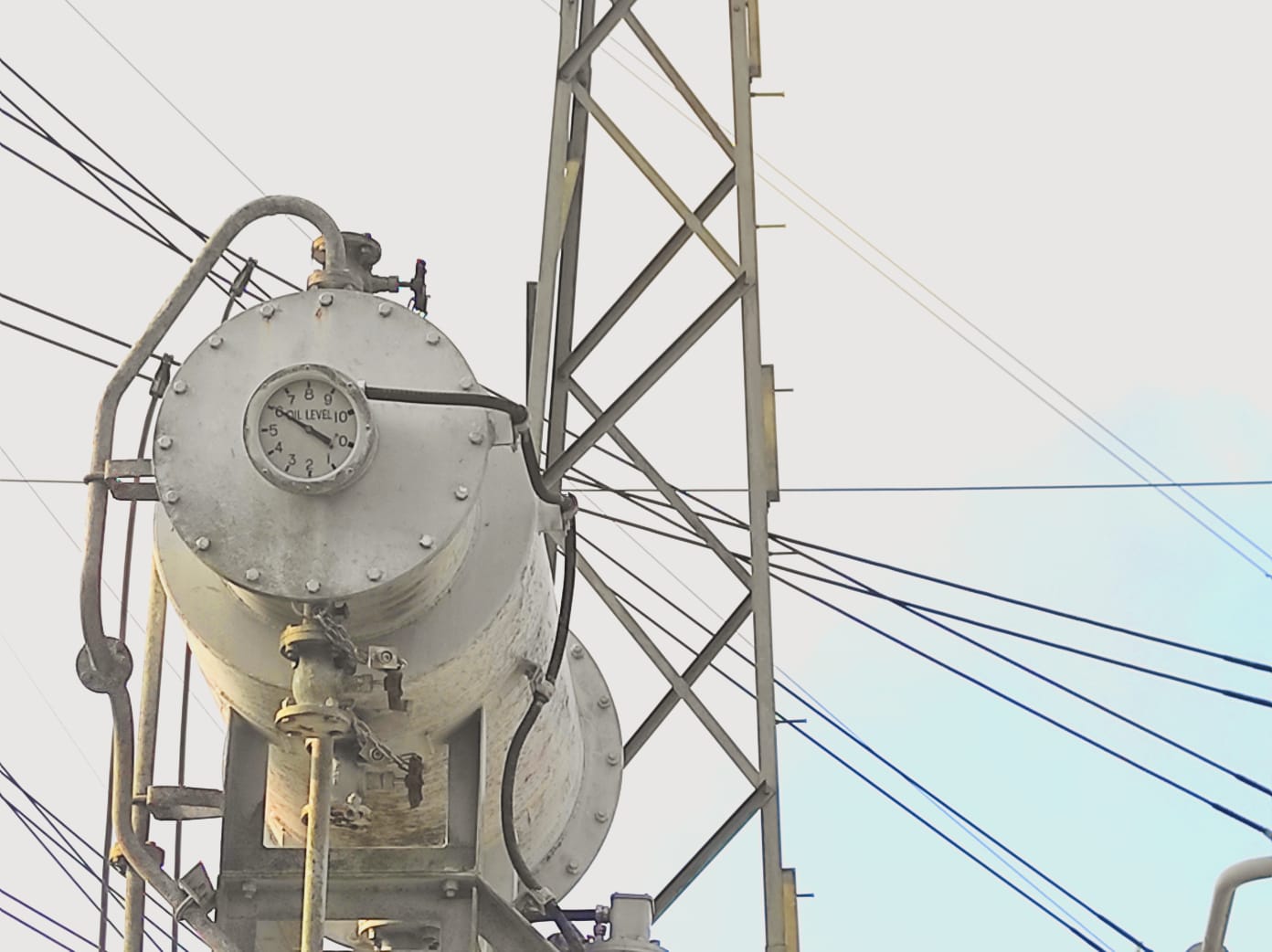
PLN UBP Kamojang
Transformer Monitoring
Early detection is useful dissolved gas analysis succeeded in finding the presence of flammable gas in the transformer, so that preventive action could be taken immediately to overcome this anomaly, avoiding the potential for much greater losses. Another implementation of smart predictive maintenance what is also done is thermograph, And breakdown voltage testing periodically.
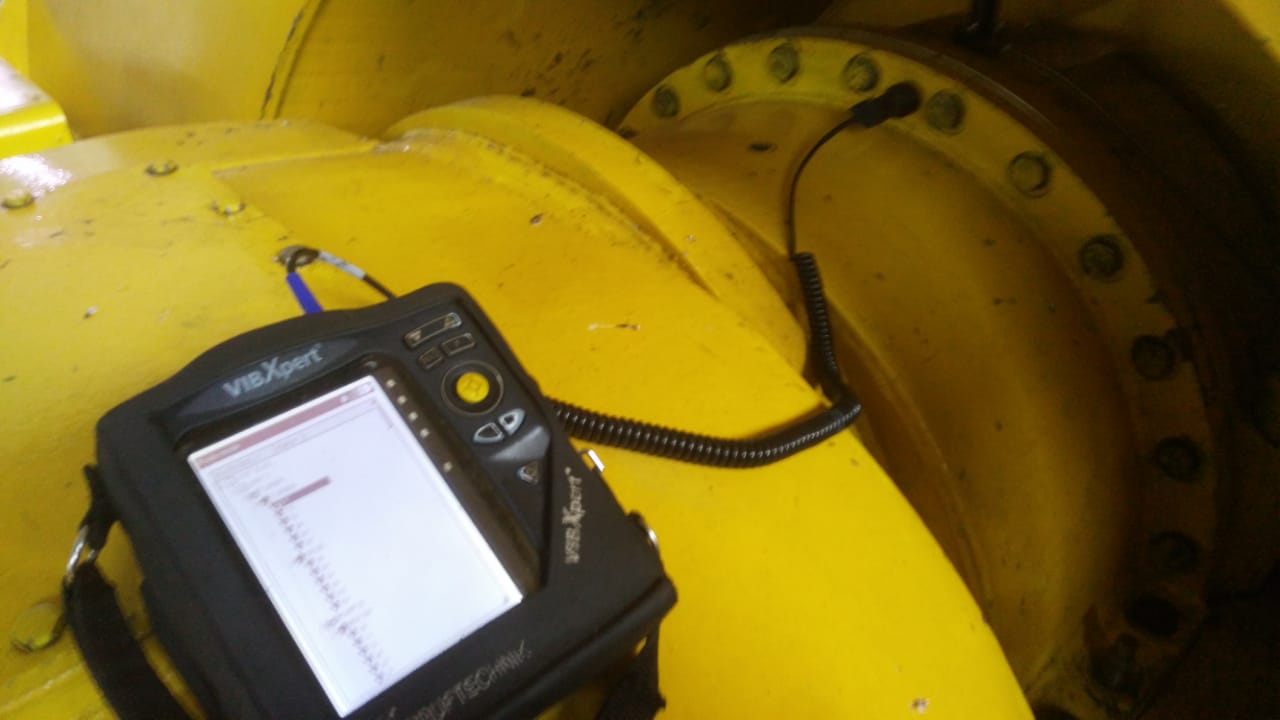
PLN UBP Mount Salak
Rotating Equipment Monitoring
Accompaniment start-up Mount Salak PLTP unit (2 x 55 MW and 1 x 60 MW) by monitoring turbine and generator vibration parameters such as vibration, to determine the turbine rotation characteristics and early detection of process anomalies starting from the process rolling up until the stage reaches maximum load.
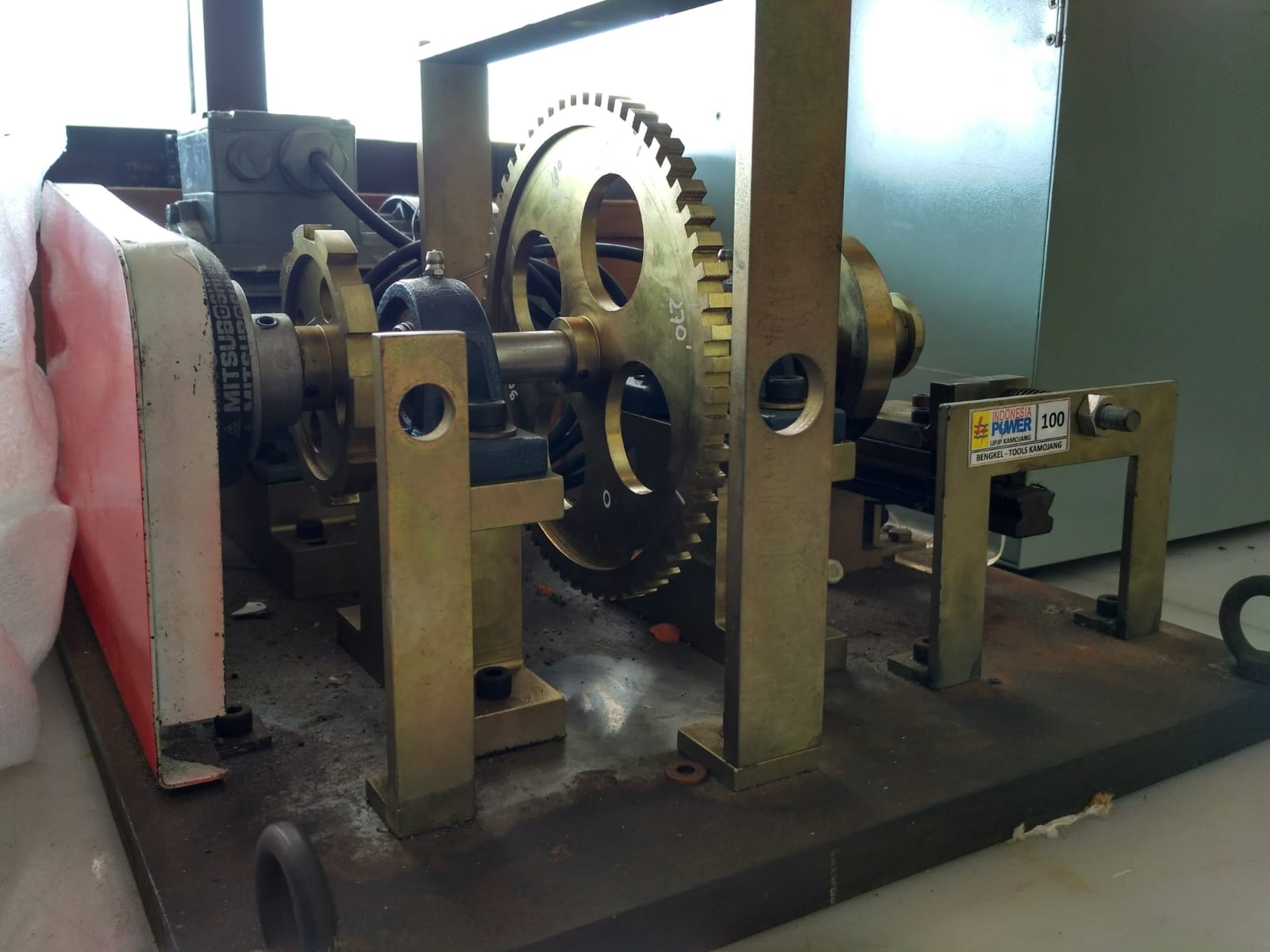
PLN UBP Kamojang
Turbine Vibration Measurement Training
Certified Kamojang Energy resource persons from the Mobieus Institute delivered a turbine vibration measurement workshop which included measurement methods, how to read measurement results, data analysis, and solving problems related to turbine vibration.
Trusted by the best
Predictive maintenance is changing the way industries operate by offering proactive insight into equipment reliability. This is not just a service, but a new breakthrough for industries around the world.